In This Story
A George Mason University systems and industrial engineering (SIE) capstone team won second place and $2,000 in the General Entrepreneurship track of the Patriot Pitch competition and won Best Presentation in the General Engineering category at the prestigious General Donald R. Keith Memorial Conference at West Point.

The SIE capstone team set out to determine the practicality of the Hexayurt, a rugged, hexagon-shaped structure made from flat, triangular panels that can be quickly assembled in areas hit with natural disasters. Hexayurts provide urgently needed temporary shelters for food storage, food preparation, healthcare services, and living spaces. The team started with a process of “customer discovery.”
“In conducting stakeholder interviews, it emerged there were several issues with these shelters,” said SIE student Ethan Ford, team lead for the capstone project. “First, transporting the materials can be expensive especially when the location is remote, or roads are no longer functional. Next, the shelters need to provide insulation from the cold or heat and be impermeable to prevent soaking up water and growing mold. Finally, it would be nice if the materials used to build the shelters had anti-bacterial properties.”
The team identified a synthetic lumber, known as Novafoam, as a potential improved material for the shelters. The lumber is manufactured by an extrusion process developed by Italian inventor Mario Gualco and project sponsor Julia Rotta.
“The synthetic lumber is lightweight significantly reducing transportation costs,” said Stephano Barra, a team member. “It also has excellent insulation properties. It is impermeable and anti-bacterial.”
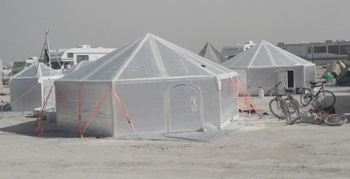
“In addition to the material properties, the Novafoam is made from recycled Styrofoam,” said team member Mickhail Ivanov. “By recycling the Styrofoam, we are reducing the load on landfills for non-biodegradable materials.”
The team documented all the stages of production from raw materials supply to pallets of finished synthetic lumber, focusing on the time-and-motion in production and the impact of fluctuations in the process. To better understand production bottlenecks, the team studied The Goal by Eli Goldratt—a classic text in operations and systems thinking. “It gave us a new perspective on balancing flow and throughput,” said team member Michael Smith.
The team also developed a detailed simulation model of the entire supply chain and production process, which “was instrumental in the design of the factory,” said team member Trevor Geisler. “The team spent hours adjusting the number and location of machines, and their parameters, to balance the flow and maximize the throughput. The final design could produce enough synthetic lumber for 2000 Hexayurts in less than 30 days.”
Team member Ethan Ford added, “The simulation model was also critically important for calculating the operating costs of the plant and the final cost of production for the lumber.”
“This project is a great example of how systems and industrial engineering can improve lives—especially in crisis situations,” said John Shortle, Systems Engineering and Operations Research department chair. “We're proud of what this team accomplished.”